Understanding Rapid Prototyping Injection Molding
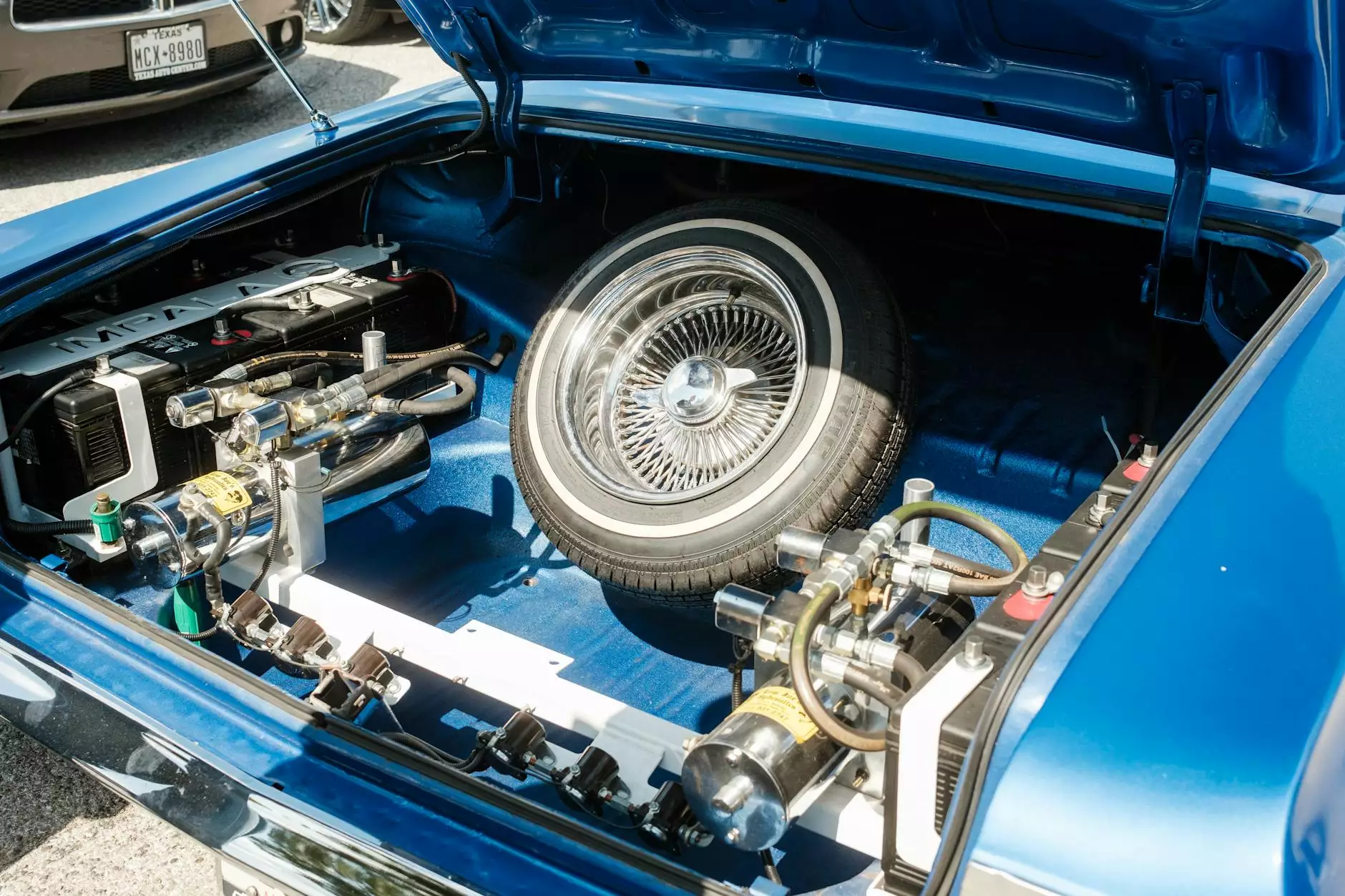
In the fast-evolving world of manufacturing, rapid prototyping injection molding has emerged as a groundbreaking approach that is not only enhancing production efficiency but also speeding up the product development cycle. This innovative method allows businesses to create prototypes quickly and affordably, making it an essential tool in the arsenal of modern manufacturers. In this comprehensive guide, we will delve into the intricate details of this technology, its advantages, applications, and how it is reshaping the manufacturing landscape.
What is Rapid Prototyping Injection Molding?
Rapid prototyping injection molding is a manufacturing process that combines rapid prototyping techniques with injection molding technology. The essence of this approach lies in its ability to produce parts or prototypes at a rapid pace, significantly cutting down turnaround times compared to traditional methods.
Typically, this process involves the use of Computer-Aided Design (CAD) software to create a digital model of the part. Once the design is complete, a prototype can be produced using various rapid prototyping techniques such as 3D printing, CNC machining, or other additive manufacturing processes. Following this, a mold is created, and the final part is produced through injection molding.
Core Benefits of Rapid Prototyping Injection Molding
There are multiple advantages to utilizing rapid prototyping injection molding. Here, we highlight some of the most significant benefits:
- Speed: The most pronounced advantage is the rapid turnaround time. Products can move from concept to prototype in a matter of days, which is critical in competitive markets.
- Cost-Efficiency: Initial investments in mold-making can be high, but the overall costs decrease significantly when producing larger volumes of a component, making it economical in the long run.
- Enhanced Precision: Injection molding offers a high level of precision with tight tolerances. This is crucial for industries that require exact specifications.
- Material Versatility: A wide range of materials can be used in the process, including thermoplastics, elastomers, and composites, allowing for varied applications.
- Iterative Design: Rapid prototyping facilitates easy modifications and iterative designs, ensuring that the final product aligns with the desired specifications and quality.
How Rapid Prototyping Injection Molding Works
Understanding the mechanics behind rapid prototyping injection molding requires a closer look at its workflow. Below is a detailed breakdown of the entire process:
1. Conceptualization and Design
The initial phase involves brainstorming and conceptualizing the product idea. Once a clear vision is established, designers use CAD software to create a digital model of the part.
2. Prototype Production
With the digital model in hand, the next step is to create a prototype. This is typically done using 3D printing or CNC machining, allowing for quick adjustments to the design based on initial testing and feedback.
3. Mold Fabrication
After finalizing the prototype, a mold is fabricated. For rapid prototyping, this can often be done using less expensive materials than traditional steel molds, such as aluminum or even 3D-printed molds.
4. Injection Molding Process
Once the mold is prepared, the actual injection molding process begins. Plastic pellets are heated until molten and injected into the mold cavity, where they cool and harden into the desired shape.
5. Finishing Touches
After the parts are ejected from the mold, they may undergo secondary operations such as trimming, painting, or assembly, which ensures they meet the final product specifications.
Applications of Rapid Prototyping Injection Molding
The flexibility and efficiency of rapid prototyping injection molding make it widely applicable across various industries. Here are some prominent sectors benefiting from this technology:
- Automotive: In the automotive industry, rapid prototyping is crucial for developing components quickly, allowing manufacturers to respond rapidly to market changes.
- Medical Devices: The healthcare sector harnesses this technology for the rapid development of medical devices where precision and regulatory compliance are imperative.
- Consumer Electronics: The fast-paced consumer electronics market uses rapid prototyping to innovate and bring new products to market swiftly.
- Aerospace: In aerospace, stringent safety and performance requirements necessitate the use of advanced prototyping techniques for component testing and production.
- Household Products: Common household items benefit from rapid prototyping, allowing designers to create functional, appealing products that meet consumer demands.
Choosing the Right Partner for Rapid Prototyping Injection Molding
Selecting the right partner for your rapid prototyping injection molding needs is instrumental in the success of your project. Here are some factors to consider:
1. Industry Experience
Look for a partner with significant experience in your industry. They will understand the specific challenges and requirements and will be more adept at delivering effective solutions.
2. Technical Capabilities
Ensure the partner has the necessary technical capabilities, including expertise in modern CAD software, advanced mold design, and various injection molding technologies.
3. Quality Control Measures
A reliable partner should have robust quality control measures in place to ensure that all prototypes and final products meet stringent quality and performance standards.
4. Customer Support
Excellent customer support is crucial throughout the prototyping and manufacturing process, ensuring timely communication and responsiveness to any project-related concerns.
5. Portfolio and References
Reviewing the partner's portfolio and client references can provide insight into their capabilities and past successes, helping you make an informed decision.
Future Trends in Rapid Prototyping Injection Molding
As technology advances, so does the realm of rapid prototyping injection molding. Here are some future trends that are poised to shape the industry:
- Integration of AI and Machine Learning: Artificial Intelligence and Machine Learning will enhance the design process, providing better optimization and predictive maintenance for molds.
- Sustainability and Eco-friendly Materials: The industry is moving towards incorporating sustainable practices, including the use of biodegradable materials and recycling waste from the production process.
- Improved 3D Printing Techniques: Advances in 3D printing will enable faster mold creation and allow for more complex geometries that were previously unachievable.
- Enhanced Automation: Automation will become more prevalent, reducing production times and costs while improving precision in the manufacturing process.
Conclusion
In conclusion, rapid prototyping injection molding stands at the forefront of modern manufacturing, offering unmatched speed, precision, and cost-effectiveness. As industries continue to evolve and demand for faster product development increases, this innovative approach will play a pivotal role in shaping successful manufacturing processes. Organizations looking to stay competitive must embrace these advanced methods to streamline their design-to-production cycles. The blend of rapid prototyping and injection molding not only enhances production efficiency but also significantly reduces the time it takes to bring innovative ideas to market.
Businesses like Deep Mould are leading the charge in adopting and perfecting these techniques, ensuring that they deliver high-quality solutions tailored to meet diverse industry needs. As we look to the future, the landscape of manufacturing will undoubtedly be changed by the remarkable capabilities of rapid prototyping injection molding.