Understanding Instrument Tube Size in Precision Engineering
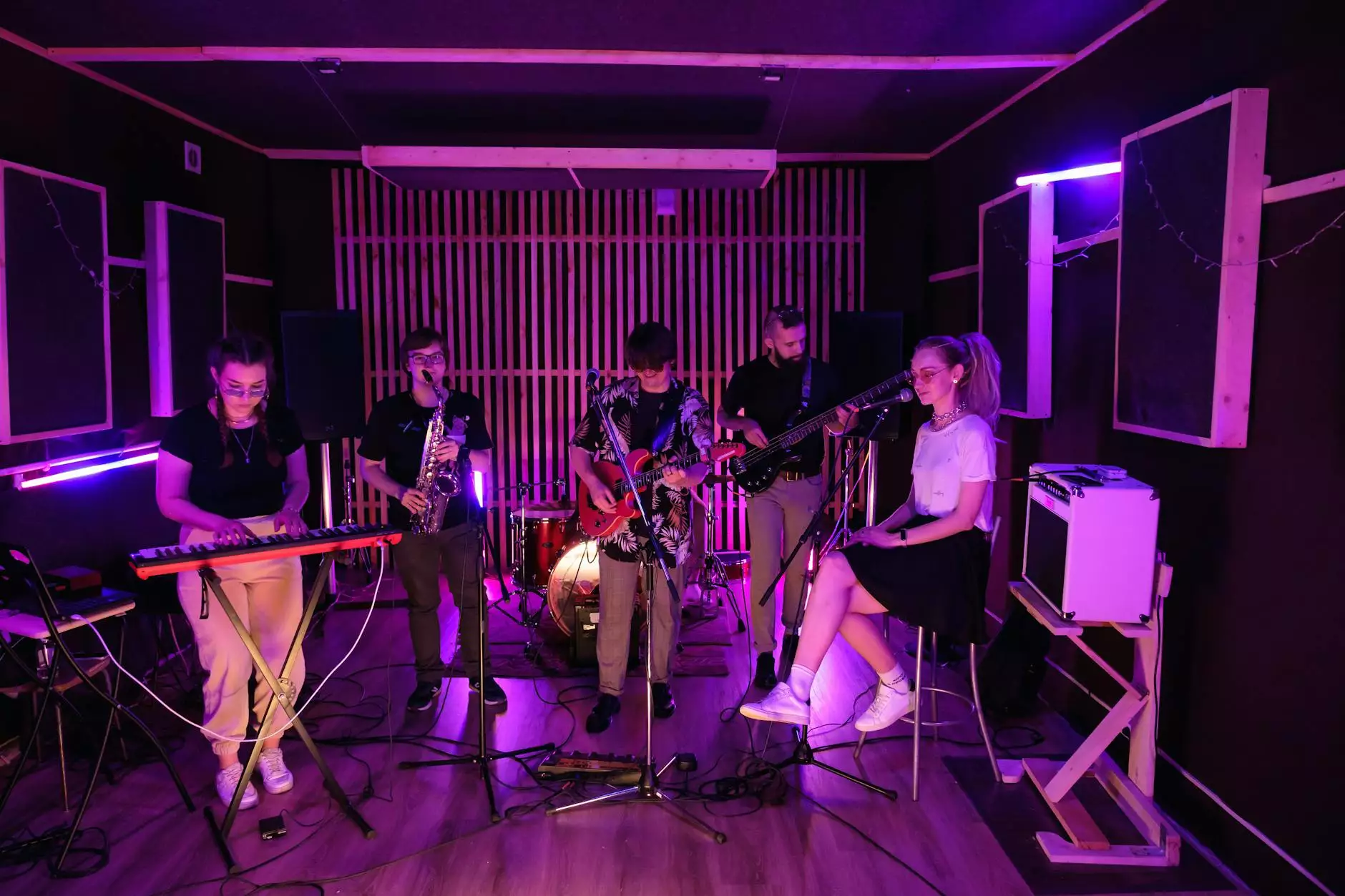
In the world of industrial manufacturing and engineering, the term instrument tube size plays a critical role in ensuring efficient and safe operations. This article dives deep into what instrument tube size means, why it’s important, especially in relation to various fittings and valves, and ultimately guides you towards making more informed decisions regarding your tubing needs.
The Basics of Instrument Tube Size
Instrument tubes are typically used to transport fluids and gases in a controlled way, often requiring precise specifications regarding size and dimensions. The correct choice of tube size is essential for maintaining pressure, ensuring safety, and optimizing performance in systems such as:
- Process control
- Instrumentation and control systems
- Fluid handling
The instrument tube size generally refers to the outer diameter (OD), inner diameter (ID), and wall thickness of the tube, which can significantly influence flow rate and system pressure.
Why is Instrument Tube Size Crucial?
Selecting the appropriate instrument tube size is crucial for several reasons:
1. Flow Rate Management
The size of the tube directly impacts the flow rate of fluids passing through it. A larger diameter allows for a higher volume of fluid to flow, while a smaller diameter can restrict flow and create pressure drops which may impact process efficiency.
2. Pressure and Safety
Using the wrong tube size can lead to safety hazards. Undersized tubes may not withstand the pressure of high fluid flow, leading to potential failures or leaks. Conversely, oversized tubes may create an unnecessary expenditure on materials and installation.
Instrument Tube Sizes and Their Applications
Understanding the common tube sizes and their applications can help in making decisions that optimize performance and safety. Here are some standard sizes and their typical applications:
- 1/8 inch: Commonly used in small flow systems for pressure transmitters.
- 1/4 inch: Utilized in applications such as pneumatic controls and fuel lines.
- 3/8 inch: Often found in hydraulic lines and instrumentation requiring moderate flow.
- 1/2 inch: Frequently used in larger systems to deliver significant flow rates.
Factors Influencing Instrument Tube Size Selection
When selecting the right instrument tube size, several factors come into play:
1. Application Requirements
Each application has unique requirements based on the medium being transported, the flow rate needed, and the pressures involved.
2. Tubing Material
Materials such as stainless steel, copper, and plastic can affect the choice of size due to their differing strength and flow characteristics. For example, stainless steel may allow for smaller tube sizes compared to plastic under the same pressure conditions.
3. Environmental Conditions
If the tubes are exposed to corrosive chemicals or extreme temperatures, this may dictate a need for thicker walls or specific materials, affecting the overall size selection.
Common Tube Fittings Related to Instrument Tube Size
To complement your tubing, various fittings are available that need to correspond with your selected instrument tube size, ensuring a seamless system. Here are some common fittings:
1. Tube Fittings
These are essential for connecting tubes securely, allowing for easy assembly and disassembly. The right fitting must match the tube's size to avoid leaks.
2. Ferrule Fittings
Ferrule fittings are crucial in compression systems, as they provide a secure seal. The instrument tube size must match the ferrule size to ensure optimal performance.
3. Forged and Threaded Pipe Fittings
Forged pipe fittings are often customized to fit specific needs. Similarly, threaded pipe fittings require precise sizing to ensure that the threads engage correctly without leaks.
4. Valves
Components like check valves, ball valves, and needle valves must be compatible with the tube size to operate effectively and safely.
Standard Practices in Selecting Instrument Tube Size
When considering which instrument tube size to choose, keep the following standard practices in mind:
- Assess Fluid Characteristics: Understand the fluid's viscosity, density, and temperature.
- Calculate Required Flow Rates: Estimate the necessary flow to ensure successful operations.
- Consider Pressure Ratings: Note the system's pressure ratings to select sizes that will withstand the demands.
- Refer to Industry Standards: Consult ISO, SAE, or ASTM standards relevant to your industry and applications.
Conclusion
In conclusion, understanding and selecting the correct instrument tube size is fundamental in achieving reliable and efficient operations in various engineering applications. As has been highlighted throughout the article, the correct size selection is vital for ensuring optimal flow rates, maintaining pressure levels, and promoting overall system safety. By considering the factors discussed and adhering to industry best practices, businesses can enhance operational efficiency and reduce costs associated with mishaps related to incorrect tube sizing.
For the best selection of tube fittings, including tube and ferrule fittings, forged pipe fittings, valves, and more, visit TechTubes.in for comprehensive solutions tailored to your needs. Experience the difference that precision engineering can provide in your industrial operations.