The Importance of Die Casting Components in Modern Manufacturing
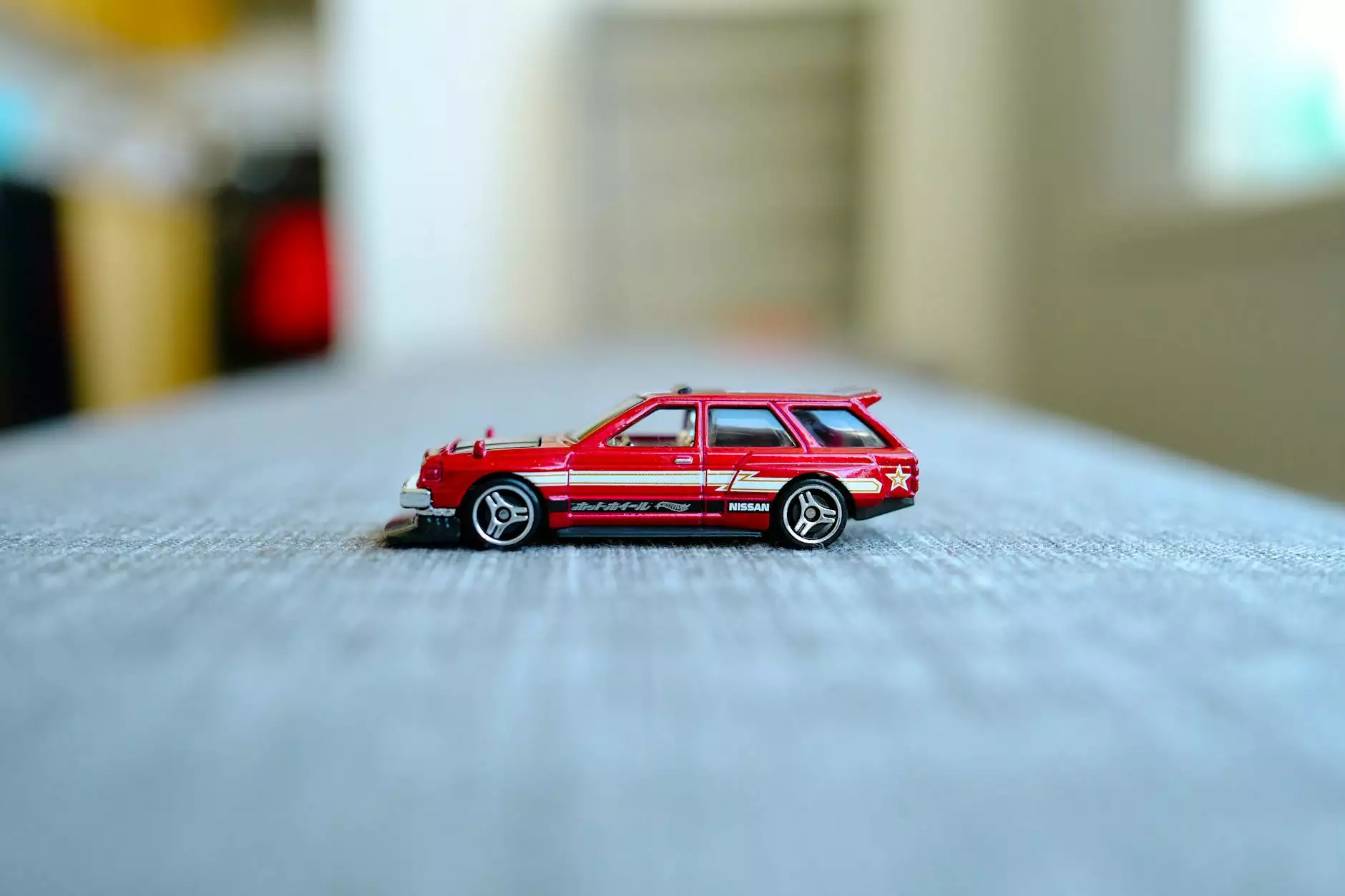
Die casting components have transformed the manufacturing landscape. These precision-engineered parts are versatile, efficient, and cost-effective, making them an essential choice for myriad applications across different industries. In this extensive article, we will delve deep into the world of die casting, understanding its processes, benefits, and the diverse applications of die casting components.
What is Die Casting?
Die casting is a manufacturing process that involves forcing molten metal into a mold cavity under high pressure. This process not only produces intricate shapes but does so with remarkable accuracy. The molds used in die casting, known as dies, can be reused multiple times, allowing for efficient production runs. The die casting process is integral to industries such as automotive, aerospace, electronics, and consumer goods.
Advantages of Die Casting Components
The popularity of die casting components can be attributed to several key advantages:
- High Efficiency: The die casting process allows for rapid production cycles, which means that manufacturers can output large quantities of components in a short amount of time.
- Precision and Accuracy: Die casting provides exceptional dimensional control, resulting in parts that meet stringent specifications.
- Cost-Effectiveness: The process minimizes waste and maximizes utilization, leading to reduced material costs.
- Versatility: It accommodates a wide range of alloys, including zinc, aluminum, and magnesium, providing options for diverse applications.
- Surface Finish: Die-cast components typically require minimal finishing, saving time and resources in post-production processes.
The Die Casting Process Explained
The die casting process can be broken down into several distinct steps:
- Melt the Metal: The desired metal alloy is heated until it reaches a molten state.
- Injection into Die: The molten metal is injected into the die at high pressure, ensuring it fills every cavity.
- Cooling and Solidification: The metal cools and solidifies in the die, taking on the shape of the cavity.
- Removing the Casting: Once cooled, the die is opened, and the finished component is ejected.
- Finishing Touches: Additional post-processing may occur, such as trimming or painting, if required.
Applications of Die Casting Components
Die casting components are utilized in various sectors, showcasing their adaptability:
1. Automotive Industry
In the automotive sector, components such as engine blocks, transmission cases, and decorative trims are commonly produced using die casting. The ability to create lightweight yet sturdy parts is critical in improving vehicle performance and fuel efficiency.
2. Aerospace Sector
The aerospace industry demands components that meet rigorous safety and reliability standards. Die casting is employed to manufacture parts like brackets, housings, and structural components that contribute to the overall functionality of aircraft.
3. Electrical and Electronics
Die casting is essential in producing housings for electrical devices and components, ensuring durability and security of sensitive electronics. Components like connectors and switchgear often leverage die casting for robust performance.
4. Consumer Goods
From appliances to sports equipment, die casting components are prevalent in consumer goods. Their ability to be molded into complex shapes while maintaining structural integrity makes them ideal for this market.
Environmental Impact and Sustainability
In today's eco-conscious world, the sustainability of manufacturing processes is critical. The die casting industry is making strides towards reducing its carbon footprint through various means:
- Recyclability: Many metals used in die casting are recyclable, meaning that end-of-life components can be reprocessed into new products.
- Energy Efficiency: Advances in technology have led to more energy-efficient die casting methods, reducing the overall energy consumption in production.
- Waste Reduction: The precision of die casting minimizes scrap and waste, making it a more sustainable option compared to other manufacturing processes.
Future Trends in Die Casting
The future of die casting components is bright, with several trends influencing the industry:
1. Increased Automation
As technology progresses, automation within the die casting process enhances efficiency and reduces human error, leading to higher-quality components.
2. Advancements in Materials
The introduction of new alloys and composite materials provides manufacturers with more options, enabling the production of lighter and stronger components.
3. Industry 4.0
Integrating the Internet of Things (IoT) into die casting operations will allow for real-time monitoring, predictive maintenance, and improved supply chain management.
Selecting a Die Casting Manufacturer
When choosing a manufacturer for die casting components, several factors should be considered:
1. Experience and Expertise
Opt for manufacturers with a proven track record in the industry. Their experience can significantly impact the quality of the final product.
2. Technology and Equipment
Advanced die casting machinery and technology can result in higher precision and more efficient production processes.
3. Quality Control
Ensure the manufacturer has stringent quality control measures in place to maintain consistency and reliability of components.
4. Customer Support
A responsive and knowledgeable support team can aid in addressing any issues that arise during production or after delivery.
Conclusion
In conclusion, die casting components are a cornerstone of modern manufacturing, providing numerous benefits and applications across various industries. Their precision, efficiency, and adaptability ensure they will remain vital in future technological advancements. Manufacturers must stay informed about industry trends and choose partners wisely to thrive in this competitive marketplace.
For businesses looking to leverage die casting technology, Deep Mould offers unparalleled expertise and a commitment to delivering high-quality components that meet your precise manufacturing needs.